Deleted
Deleted Member
Posts: 0
|
Post by Deleted on May 22, 2014 13:29:52 GMT 10
Hi everyone, I'm after some advise from anyone with some joinery experience who could possible draw me a plan or give me some advise on how I go about building a bed base to accommodate a double bed mattress with cut corners. I'm wanting to build an island double bed with lift up base to get to storage area under the bed. I was going to build it from pine and want to keep the weight down as much as possible. TIA
Mandi
|
|
|
Post by ForumMod on May 22, 2014 17:14:43 GMT 10
G'day dede, Let me search through the forum, and see what I can come up with for you.  So far I've found a few threads... 1) this one shows how masking tape was layed out on the floor to show a plan for the new layout of the van. The method might help if you're thinking of making major changes: 1969 Viscount Duralvan A49102) this one shows the island bed (on Page 3) after completion, but it will sort of show how it was done: A Coromal between Classics3) this one shows how the original steel bedframe was modified and turned into a double bed (but not an island bed): 1978 York 18ft - Y11664I know somebody else modernised the internal layout and made the island bed out of melamine sheeting. I'm still trying to remember who it was. Check out the above threads while I keep searching.  cheers, Al.
|
|
|
Post by ForumMod on May 22, 2014 17:22:06 GMT 10
|
|
Deleted
Deleted Member
Posts: 0
|
Post by Deleted on May 22, 2014 17:57:38 GMT 10
Thanks Al, will go and have a look through them now. I have worked out how to build the basic frame work without to many issues, just the cut off corners has me a bit stumped. I was going to buy a premade metal frame but getting items like that in Tassie is almost impossible, and freight is a killer.
|
|
|
Post by ForumMod on May 22, 2014 18:33:19 GMT 10
Some more threads... 1) this one isn't about the bed, but it shows some other restoration tips that you might be interested in seeing: 1976 Millard M48180 rebuild2) this one shows how the framework was done for the bed, but it's not an island bed (page 3). Also shows an option for insulation in the walls in the early pages: 1974 Viscount Royal R441403) this is another one that looks like they used melamine sheets for the framework on the bed: Chesney Regal 1969-704) and this last one shows the framework for a larger bed: Fitting a larger bedGosh there's a heap of useful information on this forum when I do a search...  dede, you can bookmark any or all of those threads, just the same as you can bookmark any other website on the internet. You can give each thread any name you like when you save it into your bookmarks. Saves you having to try and remember where you saw something on the forum "a month or more back". cheers, Al.
|
|
|
Post by ForumMod on May 22, 2014 18:52:19 GMT 10
You don't have to make the base so it has cut-off corners. Build the base as a rectangle. It's the lift-up top that gets the corners cut on it.
If I was to design a lift-up island bed for a van, I would have the base box made 3 inches narrower than the mattress base board on both sides, and 6 inches shorter than the mattress base board at the bottom end. The overhang allows you to put your toes under the vertical line of the edge of the mattress, and makes you subconsciously think there's a lot more room around the bed. A base box smaller than the mattress/lift-top will still support the mattress adequately. It means a bit less storage available in the base box, but trust me, the additional toe area around the bed will more than offset that.
The island bed in our Windsor van has the base box six inches shorter at the bottom end, but at the sides the base box is the same width as the mattress/lift-top. I'm always sitting on the bed and trying to shift my heels under the mattress line (kinda like you do when you sit on a chair and move your heels backwards under the chair). Plus when walking down the sides of our bed, my toes are always rubbing against the wall of the base box. It gives a feeling of being in a cramped space each time I do it.
Most of the stuff we've got stored in the base box is hardly ever used (it's there more for a "what if?" situation, rather than a "we definitely need it" situation). If I could make my base box smaller, I would, and just get rid of some of the junk in there.
cheers, Al.
|
|
Deleted
Deleted Member
Posts: 0
|
Post by Deleted on May 22, 2014 21:55:58 GMT 10
Thanks Al, your a wealth of information. And yes it's the lift up bit that I want to make with the cut off corners and not the base it's self. Great idea to make it that bit smaller too. As it is we will have to step over the wheel arch a little to get to either side of the bed.
Having an island bed in a small caravan has been a challenge to design the lay out of the caravan so I still have a good usable area with plenty of storage still. I'm still trying to work out how I will fit a cafe style seating area with a fold down table to make an extra bed because of the curve at the front of the van. I'm a little way off building beds and furniture yet but getting all the plans ready so I can get started as soon as the walls are back in place.
|
|
|
Post by Caprinut on May 24, 2014 20:33:22 GMT 10
Hi Dede, my van was lined sides and front with checker plate sheets sized 1200 x 2400, so I split them into sheets 600 x 2400 and got a local metal worker to bend a lip of 20mm at the bottom to wrap under the frame as a means to attach without visible screws, plus it gives a nice clean edge at the bottom to avoid injury from shin grazing etc. The lip more importantly braces the sheet, and tec screws were screwed up under the van into the frame rail. The wheel arches I marked with a tecsta from the inside to indicate the curve and then cut it with a thin graphite disc on the angle grinder at right angles to the arch and hammered it over into the wheel arch to wrap around the frame and conform to the shape of the wheel arch. This also aids in bracing and reinforcing the sides. The final effect looks clean and is waterproof as no holes allow water in. ( other than the tec screws that go in from underneath and would be self draining.) To get around the vertical join along the sides of the van you need to either position the join at the door edge or as I did in the middle at the shortest point at the wheel arch. As I had stripped the frame I positioned a wide backing frame behind where the intended vertical join would be so that the tread plate would not flex in that area and then with a good bead of silicone as a gasket behind each sheet I simply fixed it in place with a few s/steel screws to pull it tight. So far it has been without incident and I don't worry about any scrapes and stone chips anymore. The front of the van was squared up to eliminate the original curve and a full sheet of tread plate was bent 90deg in half with 600mm going up as the front wall and the other 600mm going under the van between the A-frame and floor with a thick sheet of styrene between as insulation so from the inside of the van I have an extra half meter of usable floor space that is braced and rigid. All the sheets were fixed along the top horizontal edge with a strip of J-mold alu beading that overlaps the tread lip and the screws are concealed behind the pvc insert strip. Sounds long winded but I hope it all makes sense. All the cutouts for hatches and ext shower box were cut with the angle grinder and also sealed and braced behind with a frame bead. i
|
|
Deleted
Deleted Member
Posts: 0
|
Post by Deleted on May 26, 2014 16:57:32 GMT 10
That sounds really good thanks Caprinut. Do you have any photos I can look at? I'm assuming the top of the checker plate slipped into the bottom of the Aluminum cladding? Or does your checker plate go under the cladding and attached? I think I will need to have a join above the wheel arch like you both front and back of the van, and also have the 90 degree bend to attach to the chassis underneath to keep it all tidy and secure.
|
|
Deleted
Deleted Member
Posts: 0
|
Post by Deleted on May 28, 2014 8:42:58 GMT 10
Hi all, I'm finally ready to attach the ply lining to the frame, I have a narrow crown stapler to do the job. But the old ply was attached not only with staples but glue as well in places. Should I also use glue? Or is the staples sufficient? If so what type of glue would be best?
Mandi
|
|
|
Post by ForumMod on May 28, 2014 14:17:05 GMT 10
G'day dede, The short answer is "either will do". The long answer is that "it depends"...  You would have noticed when dismantling your van that the majority of joints were stapled, whether that be when fixing panelling to the wall, or joining timber framework together. For the age of these old vans, that method has stood up pretty well (even though many of the staples rusted away where they were affected by water over time). The workers on the assembly line would have put far more staples into the van than it really required (and anybody who has tried to remove all the staples will testify to that  ). So, staples on their own do a quite satisfactory job. On the other hand, adhesives these days are also much improved over adhesives used 30 or 40 years ago, and assembling a caravan with adhesive only is also a viable proposition. When I fitted the new panelling into the Millard poptop van I restored between 2008 and 2010, I only used Selley Aquadhere exterior grade adhesive to fix the panels to the walls. No nails or staples. I sold that van a couple of years ago, but I caught up with it again recently at the Vintage Caravan event in Broken Hill, and the van still looks as good as the day I finished it (he says modestly  ). On the current vintage caravan project that I'm working on, I'm trying out a Selleys polyurethane adhesive that is 'water resistant', and I have to say I'm quite impressed with it. It's a bit pricey (just under $11 per cartridge), but it sure sticks the timber together strongly once it has cured. I have had to use nails with it, but only when fitting the ceiling sheets up into position, to hold them there while the glue cures. Elsewhere in the van I have just used the adhesive. Using staples in the panelling means you have to do something about finishing off the staple head after it has buried itself into the surface of the panelling. That means you've got to put some timber putty on the head so you end up with a nice look about the wall (and not rows and rows of staple heads staring back at you). So, in summary, you can use either. It depends on how easy it is for you to use one or the other. Using both would be a bit of overkill, but it may be necessary in certain places to do that (eg. a dob of glue and five staples might hold a part of the panelling in position, rather that just firing fifty staples into the same piece of panelling to get it to sit tight properly). cheers, Al.
|
|
Deleted
Deleted Member
Posts: 0
|
Post by Deleted on May 31, 2014 8:55:52 GMT 10
Starting the relining of the ply 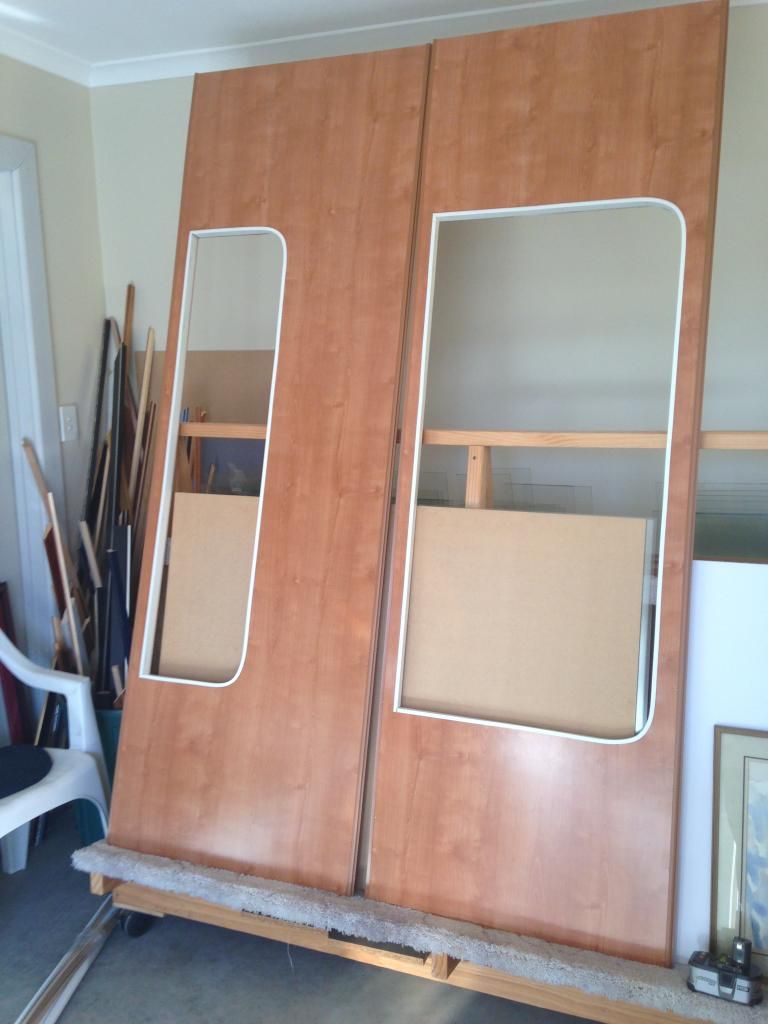 [/IMG]
|
|
Deleted
Deleted Member
Posts: 0
|
Post by Deleted on May 31, 2014 14:55:02 GMT 10
One long side completed.   [/IMG]
|
|
|
Post by murray on May 31, 2014 15:52:24 GMT 10
Dede, Looks TOO good to hide away.  Maybe you could reverse everything when you reassemble and turn into a bondwood so everybody can appreciate your work Cheers Murray
|
|
Deleted
Deleted Member
Posts: 0
|
Post by Deleted on May 31, 2014 16:45:49 GMT 10
Lol Murray, sounds like a good idea.  Well I got half the other long length done but ran out of day light, so all finished for today. Hopefully the weather is nice to me tomorrow and I can finish off the other long length. Was hoping to assemble the frame back on the chassis tomorrow but I doubt I will have time so will plan that for next weekend. 
|
|
|
Post by Sharky on Jun 1, 2014 12:10:35 GMT 10
Hi Dede good on ya having a go. I know how ya feel finding what you found I had 2 x vans I had to do major work to. 1 x was a late 70's Empire I bought knowing it had rot(bad) right hand front corner which I had to totally rebuild that corner. I had to replace the panelling under the fixed part of the roof in most places also. What I didn't count on was the poptop roof was cactus and I ended up making a total new one. I made it with slightly bigger timber but the most important thing with making a new roof is making sure the bracings are in the right spots for your lifters and lock downs. The last thing you want is to go to mount the hardware and there is no timber there where you need it. I reused the original aluminium cladding on it. I never thought I would have to do so much work on a van. Took about 6 months to do. 2nd one was a mid 80's Roma I bought. Was conveniently tucked tight in a corner so couldn't get around it, it looked ok until I got it home and pushed on the back. It had some movement in the back wall around window so I thought well its a bit rotten so I'll fix the window frame. Like you I started to remove bits to investigate and turns out there was absolutely no frame left on the rear of the van, it was totally gone. Grrrrrrr. So I had to strip the whole back of the van to rebuild the frame. Was good in a way as it enabled me to run wires etc to add extra lights and bits. It is not nice finding these problems but unfortunately a bit common with the older wood framed vans. As a reference most of the time a good indication of water ingress is your interior staples holding roof or wall panelling etc will be quite rusty. It is a pain coming across these problems but with lots of hours, $ and hard work, it is very rewarding sitting back at the end and looking at your van thinking ""I did all that"".
Love your work
Steve
|
|
Deleted
Deleted Member
Posts: 0
|
Post by Deleted on Jun 1, 2014 12:30:42 GMT 10
Thanks Steve, I know we are not the only ones who have been caught buying something with a lot of issues. Some times the previous owners don't realize, and unfortunately other times they know and patch it up so a poor sucker (me) buys it not knowing. I was ripped off and paid the price for a good van with no issues, not a van that needed a full restoration. I would love to go and see the guy that we brought the van from and tell him what I thought of his dishonesty, but that really won't help me at all. So I will soldier on and enjoy the experience. I can't imagine I will ever do a caravan restoration again, but who knows 
|
|
|
Post by Sharky on Jun 1, 2014 13:13:27 GMT 10
Yeah unfortunately there are people out there to rip you off. The Empire I knew needed work but the poor excuse for a human that sold me the Roma, would love words with him!. Whenever I have sold a van I have always told them of any problems I knew before they made their decision. You have my admiration taking on a job that size but end of it all, you will have great satisfaction knowing you did it yourself and knowing it was done right with no tradesman shortcuts! I'm no carpenter and my work is far from perfect but in my opinion nothing ventured nothing gained. Good on ya for having a go.
Steve
|
|
Deleted
Deleted Member
Posts: 0
|
Post by Deleted on Jun 5, 2014 7:27:33 GMT 10
I'm assembling the caravan frame on Saturday, bolting the frame work together and on the chassis. Originally the caravan only had nuts and bolts holding it together with some of the nuts dug into the timber and some of the roof bolts the nuts had worked their way off completely or loosened. My question is should I use washers to stop the nuts digging into the timber? Or would adding washers cause the nuts to work their way off over time with movement? Any suggestions
|
|
|
Post by Rattles on Jun 5, 2014 8:00:20 GMT 10
|
|
|
Post by ForumMod on Jun 5, 2014 8:42:14 GMT 10
Dede, in the Millard I had, the frame was attached to the chassis with really large rivets (like about 4mm or 6mm diameter). All the rest of the framework was joined together with staples - large ones for joining main pieces of timber together, and smaller ones everywhere else. For attaching your frame to the chassis, I'd be looking at using hot dipped galvanised cuphead bolts which kinda give you a bolt-head and a washer effect already built into the design of the bolt, as well as giving a longer service life with the heavy galv coating. I'd go for 8mm diameter, but you could get away with 6mm diameter if your drill set only goes up to a 6.25mm drill bit. You'd need to space the bolts a bit closer to each other if you use the 6mm size. Measure carefully the total length you need to go through the timber and the chassis, and add another 10mm for the nut and washer underneath. Don't get the bolts too much longer than the overall total length you need, otherwise you waste time threading the nut and washer up into position. Experts will say you should only have a couple of mm of thread showing after you've tightened the nut up. Anything up to about 5mm is still ok. Anything more than that means you wasted money on a longer bolt that you didn't need. Buy the bolts loose at Bunnings (ie. not in the blister packs), and you'll get the washers for the nut included in the price of the bolts (it's a Bunnings sales policy). You'll notice on the cuphead bolts that there's a square section immediately underneath the head of the bolt. You just drill the hole diameter to match the bolt shank diameter (eg. 8mm) and then push the bolt down the hole until the square bit sits on the timber. Then grab a hammer and bash the bolt cuphead down to the timber. That'll lock the bolt into position, so you can work underneath the van fitting the nuts without having the bolt spin around on the topside. Elsewhere on the framework, I'd just use screws that are galvanised and rated for external use (like this example ). Bolts aren't necessary - screws are much easier to fix, and the 50mm length will grip your timbers together quite satisfactorily. Good luck with it!  Sounds like you're making good progress! cheers, Al.
|
|
Deleted
Deleted Member
Posts: 0
|
Post by Deleted on Jun 5, 2014 21:07:13 GMT 10
Thanks guys. I'm shopping tomorrow to get the bolts, at least I know exactly what to get. I certainly don't want all my hard work falling apart.  Must add that I love this forum and all the advice I'm getting. And I'm certain there will be 100s more questions before I'm finished. I will post an updated photo once the frame is together. 
|
|
Deleted
Deleted Member
Posts: 0
|
Post by Deleted on Jun 6, 2014 13:29:13 GMT 10
I purchased all the bolts today and got Cup head bolts to join the end frames to the long frames, I had to get normal bolts to join the frame to the chassis as they go in from under the chassis and the cup head bolts wouldn't suit. And i have Phillips head bolts for the roof frame section to join the walls as they are sunk down into the timber quiet a way. I also brought all lock nuts and washers. I think I'm on the right track.  I'm organised for tomorrow now (I hope)
|
|
Deleted
Deleted Member
Posts: 0
|
Post by Deleted on Jun 7, 2014 18:08:48 GMT 10
 [/IMG]
|
|
Deleted
Deleted Member
Posts: 0
|
Post by Deleted on Jun 7, 2014 18:13:23 GMT 10
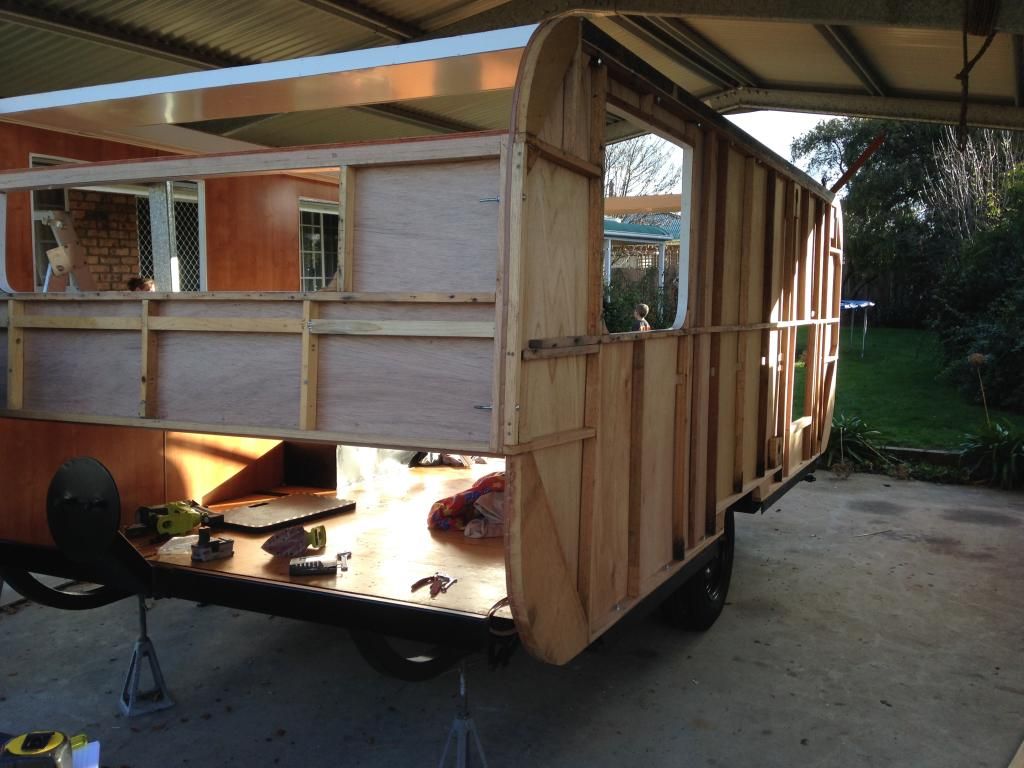 [/IMG]
|
|